The Challenge:
A manufacturing company was building 50 mobile COVID testing centers in a matter of only a couple months which required a large volume of precision weldment fabrication. The project required building 50 tubular steel chassis and associated components so that they could be assembled with the other elements at the manufacturer’s headquarters. It was a fast-paced job with lots of components and several logistics hurdles to overcome to deliver on-time.
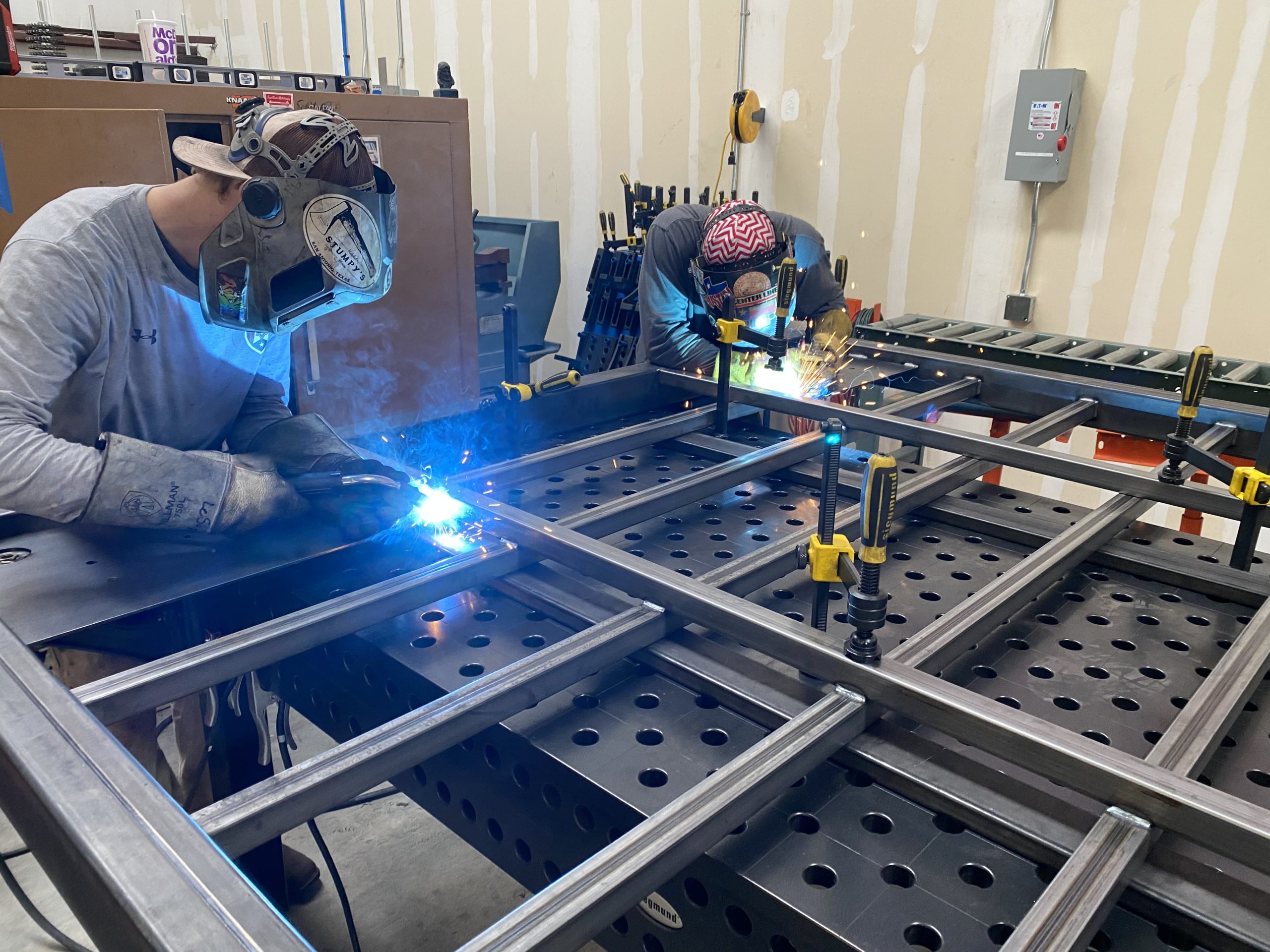
Utilizing a precision fixturing table allowed us to quickly produce highly accurate tube frame weldments
Design:
While the design of the system was nearly complete when the customer reached out, we knew that to be able to meet our customers schedule we would have to optimize the design for efficiency and quality. Utilizing our proprietary Design-Thru-Fab work flow, we modified components to include tab & slot features and laser layout lines to eliminate fit-up time and potential mistakes. Additionally we changed connection details to reduce the amount of welding required for each frame. These design enhancements would allow us to work quickly while keeping quality at its peak.
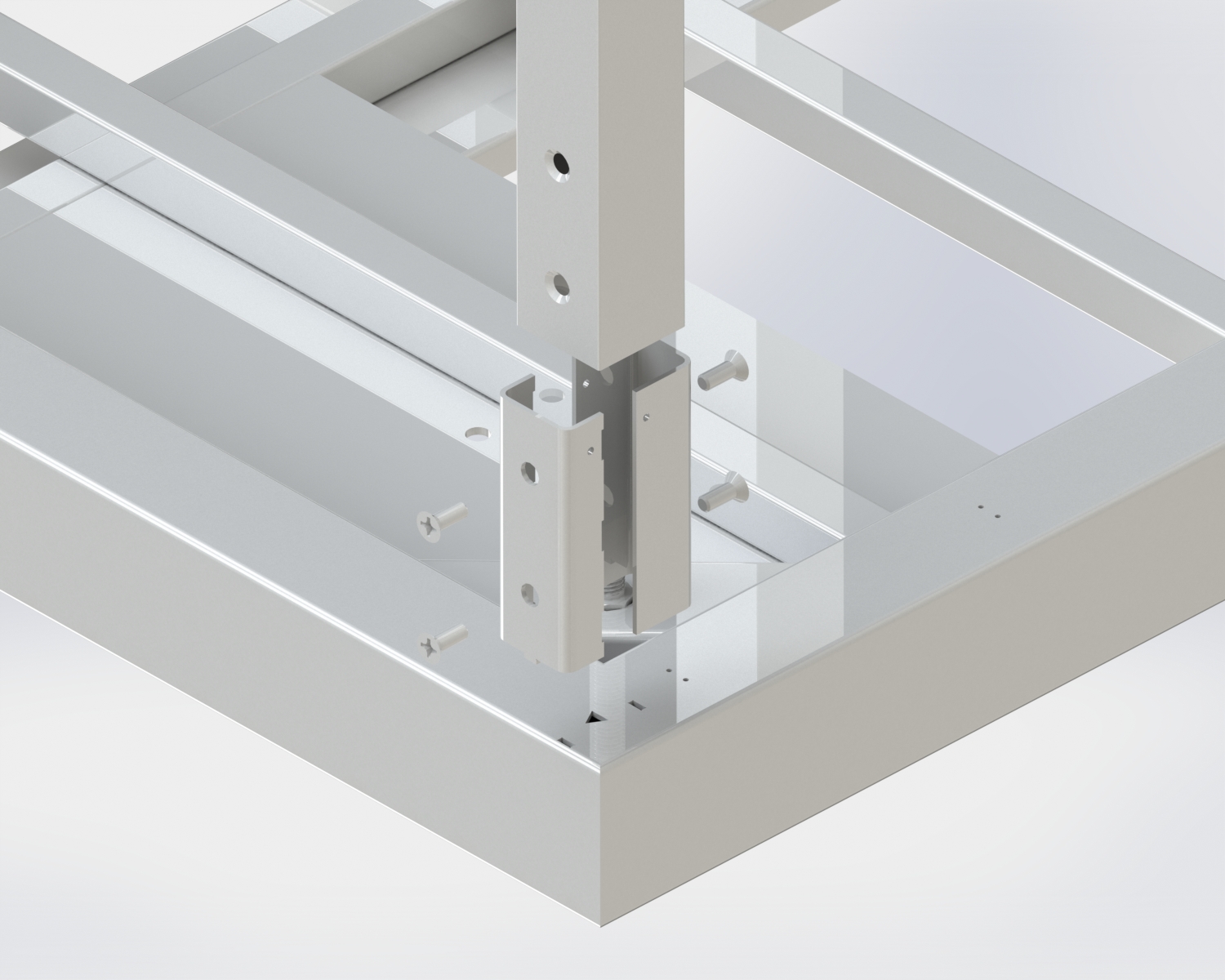
By engineering the fabrication and assembly of each component during the design phase APE is able to consistently produce higher quality parts faster.
Fabrication:
The fabrication process included laser cutting tubes, laser cutting plates, CNC press brake forming, and some light machining operations. Utilizing these cutting-edge fabrication techniques for each component during the fabrication process allowed APE to produce high quality weldments in very short cycle times.
Because we have a high precision modular fixturing table, we were able to fit the components of each frame together in a fraction of the time required by typical fabrication techniques. These fixturing tables also allowed us to easily keep a level of precision that was well within the tolerance of the project.
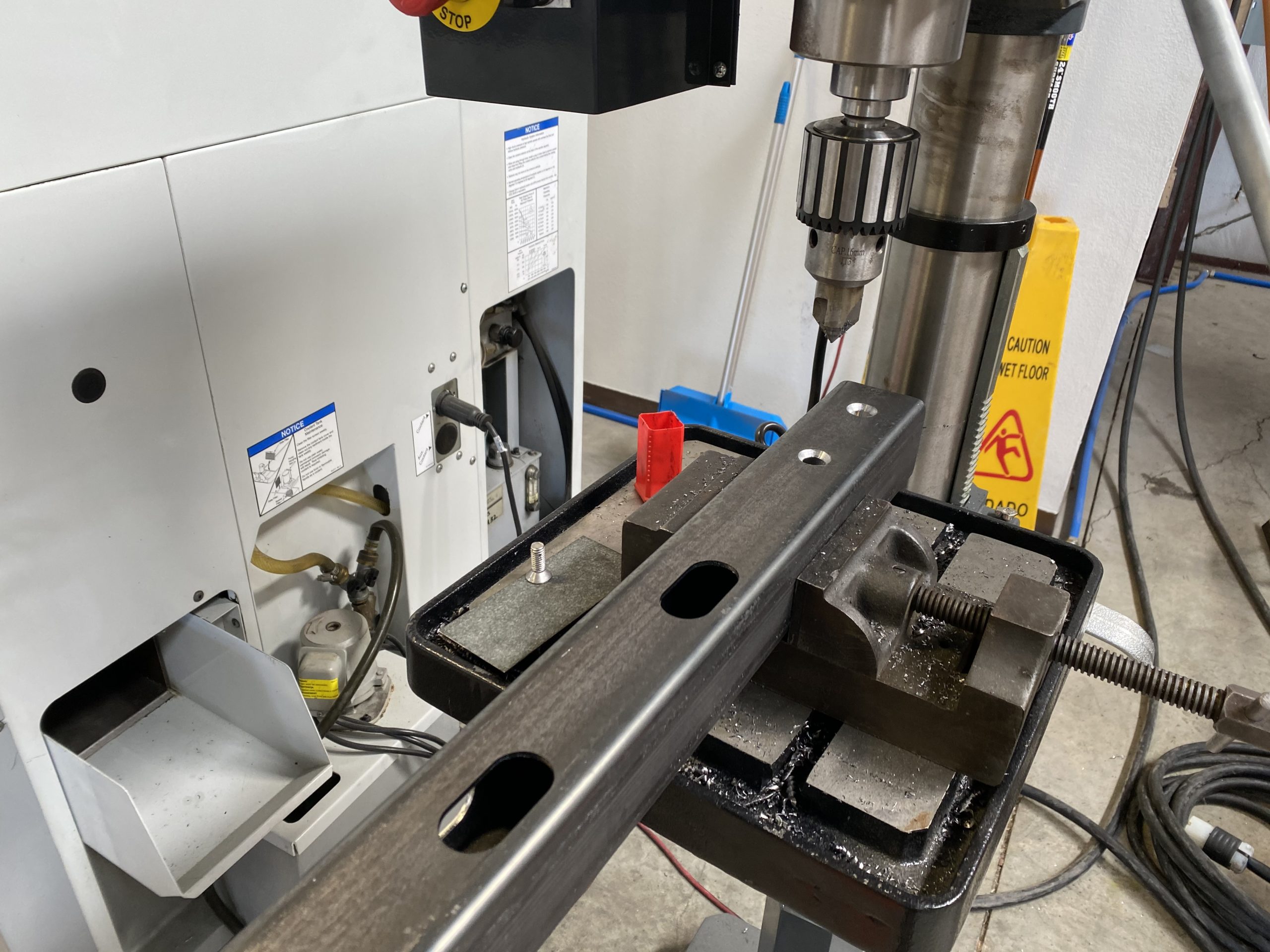
Using a drill press to countersink holes in laser cut steel tubes
The Results:
Because of APE’s innovative Design-Thru-Fab approach to custom fabrication projects, 50 frames were delivered on time to specification to the customer so they could get the testing stations deployed during a critical moment in the COVID-19 pandemic.
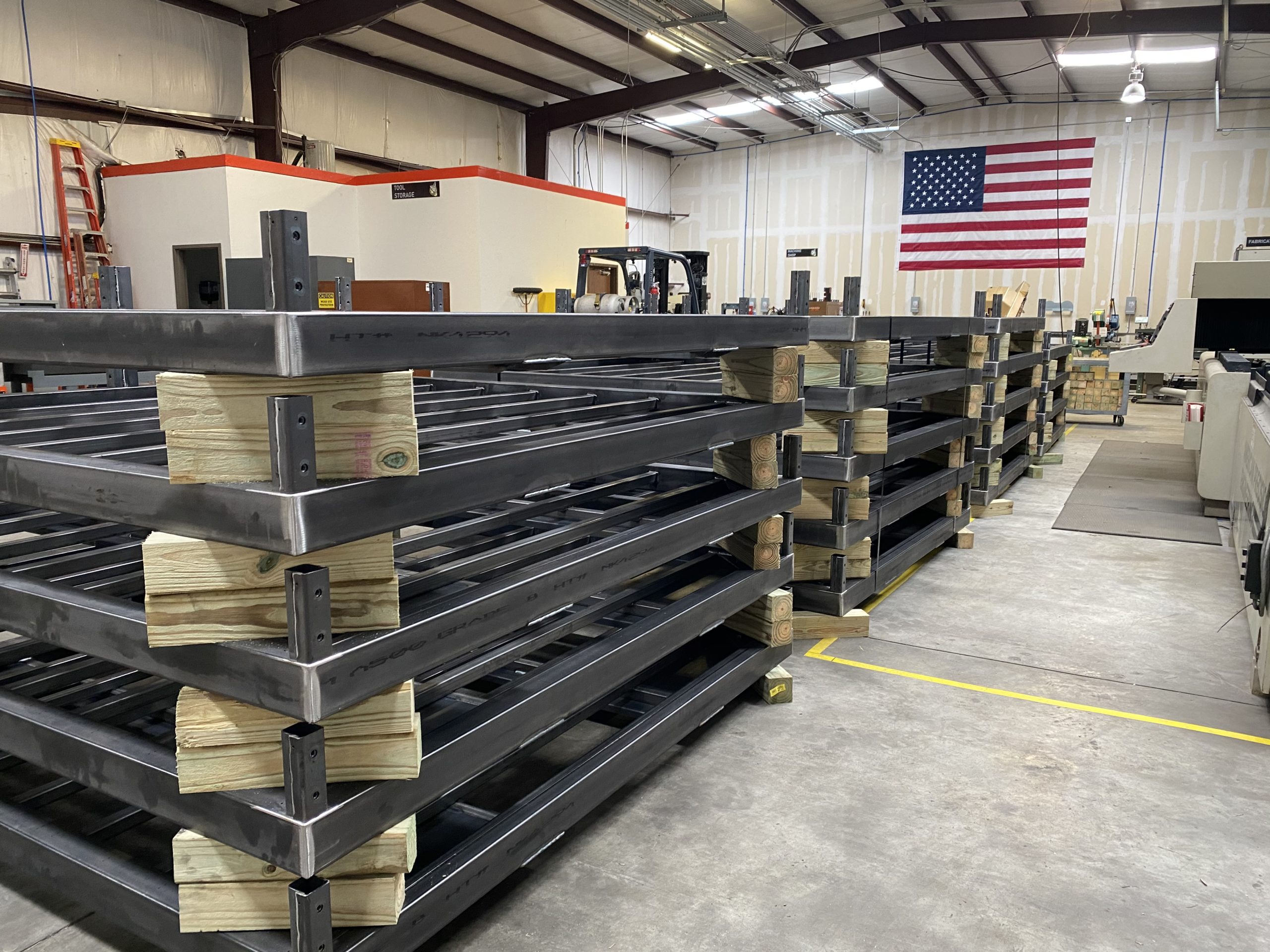
When a well engineered plan is executed with precision, large volumes of products can be produced to high quality standards quickly.